╔
Santa Catarina ports
Santa Catarina has one of the best port infrastructures of the country and the most diversified amongst the Brazilian states. There are five ports: three of public interest (São Francisco do Sul Port, Itajaí Port and Port of Imbituba), and two are of private interest (Ports of Itapoá and Portonave), in addition to other small terminals. This diversity also involves the types of cargo handled. Strategically located along the coast of Santa Catarina, the ports serve the varied economy of the State. However, they exceeded state borders, having as an area of influence, in addition to the states of the South region, those of the Southeast and Midwest regions, totaling 10 states.
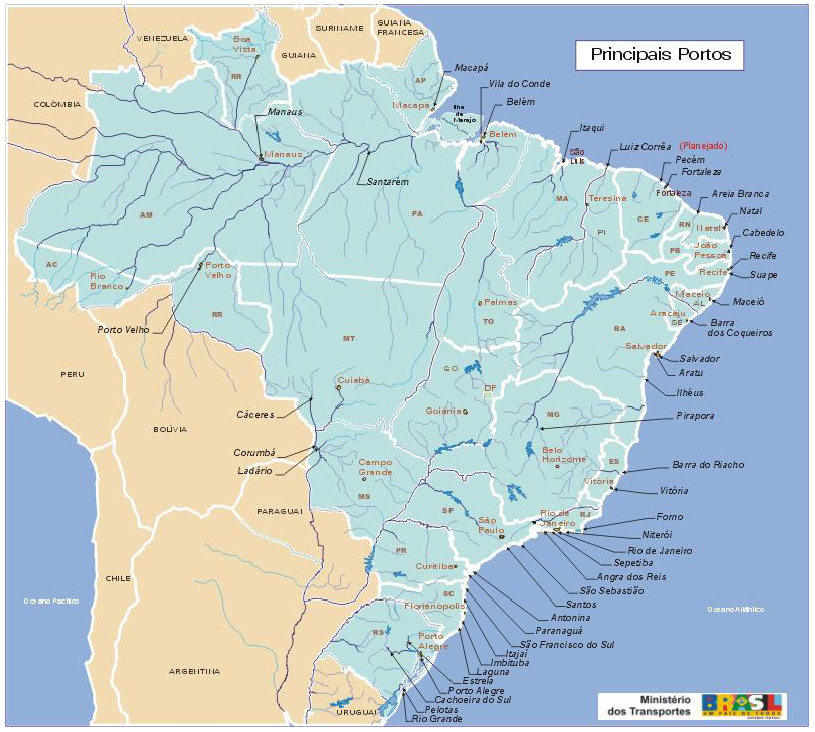
Geographical Location of Santa Catarina State, Brazil. (© Ministério dos Transportes, Portos e Aviação Civil do Brasil).
The rich and diversified economy of Santa Catarina is organized into several poles distributed throughout the different regions of the State. The North concentrates the technological, furniture and metal-mechanical poles. The West includes food production (agro-industries) and furniture activities. Serrano Plateau (Planalto Serrano) has the paper, pulp and wood industries. In the Itajaí Valley, textile and clothing, naval and technology industries predominate. The South stands out for its clothing, disposable plastics, carboniferous and ceramic segments. Greater Florianópolis stands out in the sectors of technology, tourism, services and civil construction.
It is worth remembering that the coast of Santa Catarina represents around 7% of the Brazilian coast; the population of Santa Catarina corresponds to 3.3% of the national population; and the State corresponds to 1.1% of the country’s territorial area. These indicators add even more value to the Santa Catarina port structure and the state’s competitive differentials. The participation of Santa Catarina, in the second position of the Competitiveness Ranking of Brazilian States, in the last three years, highlights the internal competencies and their importance in the national scenario.
While in the North of the State, Port of São Francisco do Sul and Port of Itapoá make use of Babitonga Bay, Port of Itajaí and Portonave use the Itajaí River, and Port of Imbituba is located in an open cove, sheltered by an 850-meter pier in the municipality of Imbituba. The export of grains and containerized cargo make the port complex of São Francisco do Sul the largest port in terms of volume transferred in Santa Catarina. On the other hand, Itajaí port complex, considered the second most important in the country, has as its differentials the reefer container cargo of high aggregate value.
The ports of São Francisco do Sul and Imbituba are multipurpose ports, that is, they handle different types of cargo, while the ports of Itapoá, Portonave and Itajaí are specialized in containerized cargo. The Port of Itajaí also handles vehicles cargo (import) in the recent years.
According to data from ANTAQ (National Waterway Transportation Agency), in the first four months of 2022, Santa Catarina handled 5.4% of the total cargo in the country. As for containerized cargo, the State handled 20.38% of the country’s cargo, which justifies an area of influence involving several regions. Thus, out of every five containers handled in Brazil, one is transferred by Santa Catarina ports.
The magnitude of the Santa Catarina port system can be observed by the nominal movement made in 2022 (data from ANTAQ): Port of São Francisco do Sul: 13.4 million tons; Port of Itapoá: 8.7 million; Portonave: 12.3 million; Port of Imbituba: 6.8 million; and, Port of Itajaí: 5.8 million tons.
In recent years, the port sector has shown a strong technological evolution. Mainly, the increase in the size of ships has been a practice of global shipowners, and Brazilian ports are already beginning to experiment the lack of infrastructure to handle such size of vessels. Thus, these deficiencies related to waterway channels are becoming evident, requiring port managers to search for investment alternatives in partnership with the private sector, since federal, state and municipal public resources will remain scarce.
Port of São Francisco do Sul
SCPar Port of São Francisco do Sul is a mixed-capital company in the state of Santa Catarina, a subsidiary of the sole shareholder SC Participações e Parcerias. It exercises the Port Authority of the port complex in São Francisco do Sul and, therefore, is responsible for managing the infrastructure and overseeing the operations of São Francisco do Sul Port.
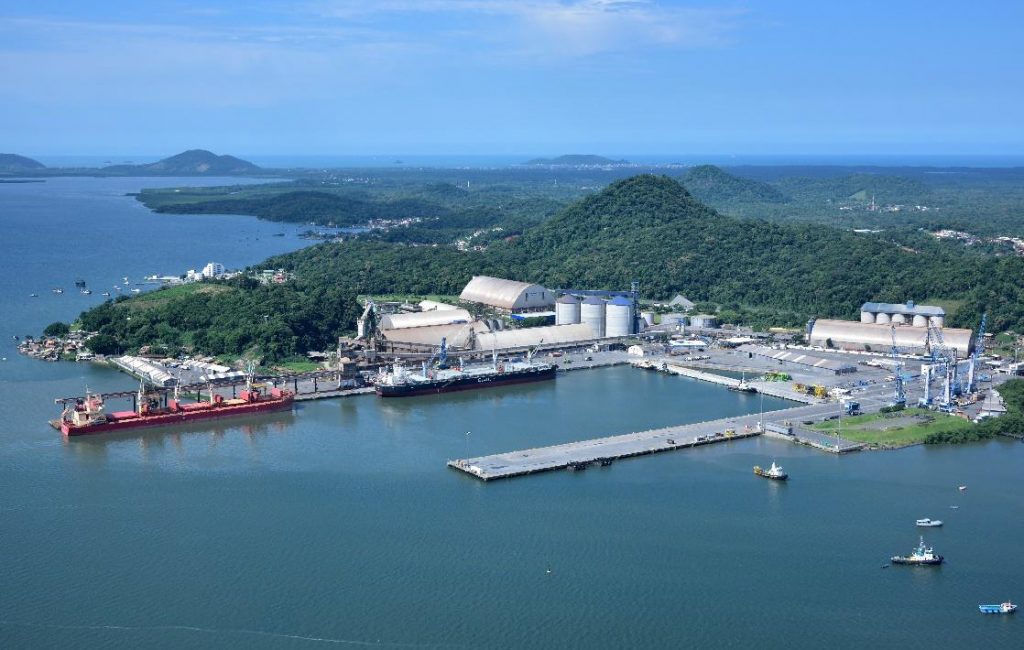
Port of São Francisco do Sul.
São Francisco do Sul Port is recognized for its dynamism and agility in operations. In large part, this is due to the partnership with large companies, such as TERLOGS and BUNGE, which make up the export corridor installed in the primary area of the Port.
The Bulk Terminal is operated by the port. It has 3 scales with capacity for up to 120 wagons and two road-rail hoppers, both with a flow of 500 tons/hour. The storage capacity is 110 thousand tons for solid bulk. The aforementioned logistics infrastructure does not include the physical structures of the TERLOGS and BUNGE companies.
Road access to Joinville, the largest city in the state, is via BR 280, a 40-kilometer route, interconnecting BR 101, which crosses the country from south to north. Railway compositions enter and leave the port via railroad 485, which connects São Francisco do Sul to the country’s rail network.
The Port of São Francisco do Sul mainly exports grains, mostly soybeans, in addition to wood. In imports, fertilizers and steel coils predominate. The volumes transferred in the last five years can be seen in the Table below.
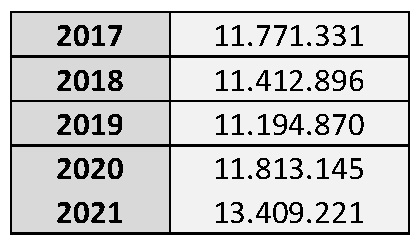
(Source: ANTAQ Data – National Waterway Transportation Agency).
As it can be observed in previous table, there is a growth of 13.5%, from 2020 to 2021, due to investments made in the port.
The practices of digitalization, automation and use of new technologies
With the objective of knowing in detail the practices of digitalization, automation and the implementation of new technologies by the Port of São Francisco do Sul, it was decided to present first, the organizational structure of the Port, listing first the end activities and then the middle activities.
Initially, it is worth highlighting the initiatives of the Port Operations and Logistics Department:
- With respect to cargo handling activities, the PortoNet System is used, which was developed by a company outside the port and is used by several port actors, supports the transactions for cargo handling at the port. In addition to the personnel of the port, other stakeholders such as port terminal operators, carriers, maritime agents, forwarding agents… use the system. PortoNet System was structured into Modules allowing each internal area or external companies to access the information of their interest and/or proceed with the proper scheduling. It is integrated with other systems, especially those of the Federal Revenue Service, which allows identifying the release of cargo that can be exported and/or exported. The scheduling of the different operations to dispatch and receive cargo at the port is also managed by this system.
- Cargo control and monitoring activities in the Port warehouses are carried out through PortoNet System.
- Vessel mooring and unmooring activities are operationalized through PortoNet System.
- Access activities to the port via gates, in addition to PortoNet System, the camera system (OCR) for reading the truck plates is also used. The integration of these systems is essential for the perfect functioning of the gates.
- Access activities for people to the port (customs area) is managed by PortoNet System through a specific module, meeting the requirements of the ISPS Code (International Code for the Security of Ships and Port Facilities).
- Control activities of the physical facilities of the port is performed with the support of 250 cameras by the Port Guard.
- Bulk Terminal activities that involve the control of grain stocks use the BALC AND PESG (Systems developed by the Information Technology sector of CIDASC- Integrated Agricultural Development Company of Santa Catarina). These systems are integrated with SISCOMEX – Integrated Foreign Trade System.
The practices of the Management Board involve:
- Bidding and contract activity a software from Banco do Brasil for conducting online trading sessions.
- People management activities, more precisely the payroll system, the SIGRH – Human Resources Management System developed and used within the scope of Santa Catarina State Government. WK RADAR System is also used, both integrated to the SFINGE system of Court of Auditors of Santa Catarina State. PortoNet System also generates information for this area.
- WK RADAR Small value shopping activities.
- Accounts Payable and Accounts Receivable activities by means of a module of PortoNet System.
- For Accounting activities WK RADAR software is used.
- For asset control activities WK RADAR software is used.
It is observed that PortoNet System is widely used by the Port of São Francisco do Sul, mainly in the final activities. PortoNet System is an Integrated System of Port Management and Administration, composed of a set of applications that manage port administration and operations, through the treatment and control of information on port activities and cargo handling, integration of information and internal and external processes.
The main characteristics of PortoNet System are described as it follows:
- The main component is the management application system, used by the Port Authority. This system is the one which process and record information on port activities and cargo handling, providing operational and managerial information and facilitating their recovery.
- The set of application systems is integrated and modular, that is, the systems work harmoniously with each other, exchanging information and avoiding rework, using a unified database.
- The system has no limitation on volumes and users.
- All functionalities are managed through a specific application that controls and manages accesses and permissions and links them to the functions and applications, which can be configured according to the need and organization of the Port and the users’ profile.
- The control and management of access and permissions is integrated into the System, so that a set of operations can be performed for each user, according to the profile of the same, with management by module or application and function, in addition to allowing the record of operations carried out and their auditing.
- The permission of access to the System is given to the users or groups of users at the application and/or function level. It gives access data to the specific users that has the right to use such data.
- The system integrates several members of the port community, such as Antaq, Brazilian Federal Revenue, Terminals, Port Operators, Maritime Agents, Unions, Carriers and others, electronically.
- Whenever possible, the data entry occurs in the origin of the information in order to minimize transcription errors and internal work.
- The system has an online manual with description of functions and attributes in all the system’s operating modules.
- The applications currently available suffer, in most cases, adjustments and adaptations due to fiscal, legal, economic and operational needs, to meet them.
- Apps are implemented for the web environment.
The architecture used by PortoNet System is open, implemented in a graphic platform, allowing connectivity with different technologies. Applications that compose PortoNet System uses Web technology (Internet) with free software. All new developments must be specific, modular and integrated with the current system, using free software, PHP language, Apache web server, as well as browsers on client stations.
The main tools used in the development and maintenance of the software are: (i) PHP 5 programming language, with jQuery Library, iReport, Jasper and Zend 1 (frameworks); (ii) PowerDesigner case tool (template); (iii) BizAgi BPMN process modeling tool; and, (iv) Apache web server.
The Database used is SQL Server 2008 Standard Edition. There are two environments with databases: one for testing, including support, maintenance and development, and another for production, where the corporate database used by PortoNet System is located.
It contains the description of PortoNet System modules adjusted or developed in the different phases of the Port of São Francisco do Sul Computerization Project, for port management. The main modules are as follows: Access to the System; Vehicle scheduling; Registrations; Dangerous Loads; Invoicing; Gates; Indicators; ANTAQ Integration; ISPS Code Integration; Port Operator Integration; Porto Sem Papel Integration – PSP; Radar Integration; Redex integration; Unions Integration; Port Terminal Integration; Port Operation; Port Operation – Storage; Port operation – Electronic Manifest; Port Operation – Weighing; Port; Graphical panel; Programming of Vehicles; Traceability; Data and Information Retriever; Port Departure – Gates; Treasure-house; Vessel Traffic; Transit Leaseholder; e, Screening.
PortoNet System was an initiative of the Port of São Francisco do Sul to use a system developed specifically for the ports, being used in other Brazilian ports, such as the Port of Rio Grande, state of Rio Grande do Sul.
Since 2011 the Port of São Francisco do Sul implanted the Porto Sem Papel – PSP. Porto sem Papel is an information system whose main objective is to gather in a single platform or system, the information and documentation necessary to speed up the analysis and release of goods. Around 140 paper forms have been deleted and converted to a single electronic document. Less bureaucracy, more agility and economy.
Following recommendations from the International Maritime Organization (IMO), the system acts as a port single window tool. The person responsible for the vessel, the shipowner or the shipping agency provides the mandatory and necessary information for the entry or release of the goods in a single database. From this, it is possible to analyze the data by the port authorities and the supervisory bodies.
All information is available in a single database, in a safe and accurate way, allowing a more efficient management of available resources and contributing to the improvement of processes in the port sector.
The single window concept can be defined as a facility that allows those involved in trade and transport to standardize information and documents, with a single entry point to fulfill all import, export and cabotage, and regulatory requirements. If the information is electronic then the individual data elements should be informed only once.
In practice, the adoption of the “single window” reduced the time required for berthing and vessel´s service operation consents granted by the various inspection bodies that work in ports. The system therefore sought to streamline procedures. As such, a single window allowed companies to submit information (declarations, electronic consents for vessel stay and other justified documents such as certificates of origin and invoices) to regulatory bodies in a single transaction and/or in a single entity.
In a traditional environment, the port needed to exchange information with multiple government agencies in order to obtain the necessary papers, licenses and permits to complete its import, export and cabotage processes.
As there is a single window for data entry, this implied an increase in efficiency, both in terms of reducing the time for berthing and vessel´s service operations, and in reducing the costs of companies in their transactions with various government authorities to obtain permits and licenses for the export and import of cargo.
Porto Sem Papel (PSP) was a strategy of the Federal Government of modernization and digitization of ports. Its implantation initiated by the Brazilian ports in 2011. Due to the advantages of the project, most of the ports accelerated its implementation.
Among the Santa Catarina ports, the Port of São Francisco do Sul is the most digitized, as it has implemented advanced digitalization and automation initiatives and is constantly improving its operations. The ports of private interest (Itapoá Port and PORTONAVE) have higher levels of digitalization and automation, given their characteristics, but mainly due to their corporate ties to MAERSK and MSC shipowners.
Final considerations
The Port of São Francisco has digitalization and automation processes that can be considered advanced, with emphasis on corporate systems widely used within the scope of the Port.
Noteworthy are PortoNet System and Porto sem Papel, which allow the digitalization and automation of the main activities carried out by the Port, mainly impacting on the Port’s operations and logistics, that is, on the core activities.
Challenges still exist and can be listed as priorities: (i) definition of a strategic digitalization and automation policy for the port; (ii) expansion of the integration of PortoNet System to other port areas; (iii) integration of activities between the various systems used within the Port; (iv) expansion of automation of routines and procedures currently developed in office software.
Thus, the Port of São Francisco do Sul is inserted in a process of digitalization and automation. However, this process needs to be improved considering customers and port actors at the heart of the company’s strategy, a sense of urgency for constant changes and a new leadership profile.
HEAD IMAGE | Port of São Francisco do Sul.